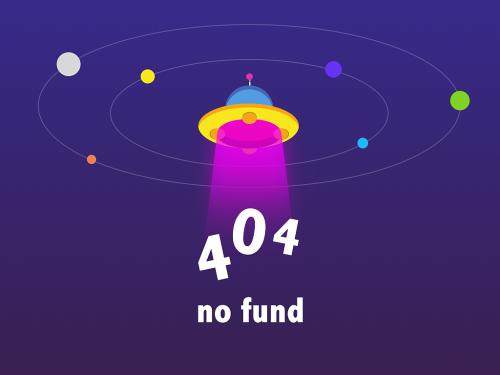
“十一五”以来,重钢结合自身实际,“产学研”相结合,加强原始创新、消化吸收再创新和集成创新。从自主集成高炉、炼钢工序、热连轧和大公辅等某个单元,到自主建成现代化全流程钢铁厂,重钢一直担当着推进重大冶金装备自主创新和国产化“领跑者”的角色,在敢“闯”和敢“试”中引领钢铁项目建设新变革,走出了一条“高起点、少投入、快产出、高效益”的具有中国特色的钢铁工业自主创新之路,跨入国内先进钢铁企业行列。
重钢改革发展的“活源泉”--思维创新
传承着中华民族钢铁工业血脉的重钢,在建国之初为新中国成功轧制出第一根钢轨,带着十大钢铁企业的昔日辉煌,在21世纪却遭遇着更为现实的严峻挑战:在资源上,开发力度不够、过分依赖进口;在环境上,治理跟不上越来越高的环保要求;在规模上,受困总图、与重庆市区城市拓展矛盾突出。
重钢的出路在哪里?永不向命运低头的重钢人,用全新的思维在努力寻找着答案。重钢集团党委书记、副董事长张再坤说,“十一五”初,根据对形势和自身的正确判断,重钢集团领导班子以科学发展观为指导,承担使命,集思广益,在重庆市委、市政府以及市国资委的支持下,下决心打破发展受限的“宿命论”思维定势,确立了“自主创新、开发资源、环保搬迁、优化结构、做精做强”的加快企业发展的战略思路。
思维决定思路,思路决定出路。启动环保搬迁只是万里长征的第一步。接下来,环保搬迁究竟如何搬?到底要建设一个怎样的重钢新区?这是全市人民期待重钢作出的必答题。
力争建设世界标杆钢铁企业的思路悄然浮出水面。环保搬迁全过程中,重钢始终贯穿“清洁生产、节能环保、发展循环经济、建设生态钢城”的设计理念,通过技术创新,以流程优化为基础,以节能减排为重点,依托高效化的信息平台,努力建设“钢铁流程现代化、工艺装备大型化、企业管理信息化、组织架构扁平化”的现代钢铁企业,成功实现向资源节约、环境友好型企业的转型。
思维创新的闸门,一旦开启便一发不可收拾。重钢集团以环保搬迁为契机,全面技术改造、升级换代,继而明确提出要实现千万吨规模、千亿元销售收入的“双千”目标;建成中国乃至世界最大的船用钢精品生产基地;中国最大的江海物流及船用钢材加工配送基地;中国乃至世界最大、最先进的环保产业;成为党建、精神文明建设、尊龙最新版的文化建设最具特色的企业;构建和谐社会、建成职工幸福感最强的企业。
重钢科学发展的“强引擎”--技术创新
面对市场“寒冬”,技术创新是钢铁企业坚守阵地、打造核心竞争力的“底气”所在。重钢集团总经理、副董事长、党委副书记赵世庆说,重钢必须坚持把技术创新作为“原动力”,靠以企业为主体的自主创新,推动产品向特色化和效益化方向发展。
“十一五”以来,重钢围绕生产经营中的难点,加大科技攻关的力度,重点抓好铁前系统、炼钢技术指标的改善,抓好船用钢品种开发,抓好煤气利用与煤气发电,重点强化炼铁喷煤攻关,深化炼焦配煤、烧结配料研究,挖掘轧钢设备及工艺潜力,全面改善各项技术经济指标,实现对高炉渣、钢渣、含铁尘泥、煤气、工业废水和余热蒸汽的闭路循环利用。2011年,重钢按照突出重点、少而精的立项原则,先后组织专家进行科技项目立项论证,下达集团科技项目计划6批29项、总投入2184万元,共获市区政府资助资金300多万元。
此外,重钢还通过“产学研”结合,借脑引智,有效地解决了企业在技术研发工作中存在的技术难题,提高了企业技术创新能力和科研水平。引进博士后开展了《垃圾焚烧发电厂渗滤液的污染控制研究》等近10多个项目的研究;与北京钢研总院、重庆大学、重庆科技学院等高校院所进行战略合作,开展《提高重钢新区高炉喷煤比的研究》等70多个项目的研究。
近年来,重钢通过技术创新评价、政策引导和宣传培训推动多种形式的群众性技术创新活动,建立了以专利为主线的知识产权管理和创新体系,并取得了显著成效。十年来,共申请有效专利498件,其中发明专利95件。
环保搬迁启动以来,重钢专利质量明显提高,新区建设集企业自主技术创新成果之大成,拥有自主知识产权43项,引领冶金制造流程革新的铁-钢界面“一罐制”和rh干式真空技术创新应用成效十分突出,真正实现铁钢界面紧凑式布置,大大降低能耗和污染排放,大幅降低建设投资和减少占地面积,在冶金行业具有广泛的推广示范效应,对我国钢铁工业发展具有深远的影响。其中“重钢首次将机械泵应用于rh精炼工艺” 2011年荣获中国冶金科学技术一等奖、被评为世界钢铁工业十大技术要闻,围绕此工艺技术重钢先后申请15件专利加以保护;重钢拥有自主知识产权的“余热综合利用的钢铁联合装置”获得实用国家新型专利。
“十一五”以来,非钢产业技术创新方面也是亮点纷呈。矿业公司西昌矿业从举步维艰的困难企业摇身变为国家高新技术企业,成为全国唯一获“国家高新技术企业”殊荣的矿山企业,目前正在全面启动钒钛资源综合利用研究;三峰环境在主编《生活垃圾焚烧炉及余热锅炉》国家标准的基础上,赢得“国家环境保护垃圾焚烧处理与资源化工程技术中心”的正式落户,进一步确立了重钢环境产业在生活垃圾处理行业的技术领先地位;重庆钢铁研究所公司走出了一条拥有自身专业特色的发展之路,成为国内航天材料和航空管材的主要生产基地,其研制的航空航天新材料助力天宫一号太空寻梦;朵力地产首创以“成建制交房交证”为核心的诚信经营“六步法”,在全国树立了诚信地产标杆和榜样。
重钢自主发展的“试验田”--流程创新
“重钢新区开创了世界钢铁企业厂内无铁路运输的历史,真正实现了钢铁流程简单化、紧凑化和准连续化。”重钢集团副总经理董荣华向《中国冶金报》记者介绍。
重钢新区可循环钢铁制造流程,大胆地突破传统,采用闭环式生产,把清洁生产、资源综合利用和可再生能源开发融为一体,实现钢铁产品制造、能源转换、废弃物处理消纳三大功能,呈现“采用高效化工艺、生产高质量产品、实现高清洁生产”的“三高”态势。这有别于传统钢铁流程中物质单向线性流动、开放式生产、仅能实现钢铁制造功能等特点,从而较好地规避了传统钢铁流程制造过程中成分、温度波动大,资源能源利用效率低,污染严重等不利因素。
新重钢总图运输快捷顺畅。根据地形的特殊状况,新区充分利用了地形、地势,总平面布置与自然场地的有机结合、场地竖向采取多台阶布置,达到工程量省、建设快,长期运营费用低的目的。目前新重钢吨钢用地指标达
重钢以环保搬迁为出发点,结合自身实际,创造性的开发了“平车 吊车”的“一罐制”技术。这技术是指直接采用炼钢铁水罐运输铁水,将铁水的承接、运输、缓冲贮存、预处理、兑铁、容器快速周转及铁水保温等功能集成为一体的技术。
“一罐制”技术设计上取消了混铁车运输中约
另外,虽然重庆身处内陆,但长江黄金水道以及公路、铁路运输系统发展较完善。对于我国内陆大型钢铁联合企业而言,同时具有江河、铁路、公路三种运输方式的企业不多,重钢新区有此优势,为减少物流成本创造了条件。新区采取皮带、管道、辊道等运输方式的综合使用,厂内、外道路运输总量可达2075.4万吨,吨钢物流运量比为1:3.2,远低于通常厂内吨钢物流运量比1:6,且物流更为顺畅、成本大大降低。
重钢转型发展的“助推器”--工艺创新
重钢新区炼钢环节采用的rh真空精炼工艺,具有脱氢、脱碳、脱氧和提高钢水成分及温度的功能,对品种的开发和提升钢水质量具有重要作用。2012年元月4日,《世界金属导报》公布2011年世界钢铁工业十大技术要闻,“重钢首次将机械泵应用于rh精炼工艺”位列第5。这是重钢技术首次站上世界钢铁工业技术舞台的前沿。
之前,该技术成果荣获了2011年由中国钢铁工业协会、中国金属学会颁发的中国冶金科学技术奖一等奖。董荣华向记者介绍,重钢这套 rh机械真空冶炼系统由19组(1组备用)双排并联的机械真空泵组成。采用72台机械泵组成18个真空模块,每个模块由4台三级机械泵组成。根据工艺需要控制18个真空模块的运行,以达到rh工艺对真空度的要求。
谈到这套装置的运行效果,董荣华兴奋地对向记者讲,该装置目前生产运行效果明显,优于相同规格的蒸汽喷射泵系统的工艺指标。例如,脱氢率达63.5%、极限脱碳能力为10ppm、运行成本(包括电能、氮气和补偿冷却水)较蒸汽喷射泵系统低7.74元/吨钢。
取消厂区蒸汽管网,开发应用先进的节能技术,在低温余热资源等二次能源利用方面做足文章,则是新重钢在自发电领域进行地工艺创新和大胆尝试。重钢借鉴、参考、选择了国际国内先进钢厂二次能源利用方式组合经验,从焦化厂干熄焦发电技术、炼铁厂trt余压余能发电技术到烧结、炼钢、轧钢各工序余热资源的综合利用发电技术、ccpp发电技术,这些先进技术的优化组合,使重钢新区二次能源得到了高效优化的利用。
正是利用分布式低温余热电站的建造模式实现了无全厂性的蒸汽综合管网,消除了其运行、维护及蒸汽使用调度等繁杂的工作,这在国内的钢铁企业中也是一次创新,一个新的建厂理念。董荣华说,到今年底,重钢新区将有21台发电机组,全部利用生产环节的余气、余热、余压发电,自发电量将占到全厂区总用电量的70%。
“根据中钢协统计,目前国内还没有一家钢铁企业,自发电比重达到70%。”董荣华称,这一指标已达到世界一流水平。届时,重钢每年自发电量将达到17亿千瓦时,除去发电成本,每年可节约电费5亿元。
作为重钢环保搬迁的重要内容,此举更重大的意义在于保护环境,减少排放。按照国际标准计算,每节约1千瓦时电,就相应节约了
先进的循环用水系统则是重钢新区工艺创新的另一大特色。其一,充分发挥新区钢韵湖的库容,实现移峰填谷的作用。利用地形高差的优势,取水站所集中在电价谷段和平段向钢韵湖输水,而在尖峰和高峰段停止取水,使用钢韵湖储存的源水自流到中央水处理站进行净化处理,从而实现节约取水电费的目的。其二,地下渗水回用,拓展回用水用户,减少新水消耗。中央水处理站处于厂区最低位置,在该平台和护坡已发现大量的地下渗水且满足回用水的原水水质要求,因而通过对该类水的收集,转供回用水用户,能够减少回用水制备的药剂消耗,保证回用水有充足的源水供应。其三,利用水温差和地势差,综合进行排水系统的改造,做到分级用水和分质供水。各空压站蒸发空冷器喷淋系统,为降低浓缩倍数每年要排放4.8万吨的喷淋水。而就近的余热等站所净环系统又要频繁补充生产新水,由于空压站的喷淋系统位置较高,通过敷设管道把空压站的排水回收作为余热等用户的补水,从而降低新水耗量。经记者调查,焦化厂废水稀释使用的是生产新水,本着分质供水的原则,拟对该系统的补充水进行改造,使用全厂回用水替代,每年可节约新水消耗61.32万吨。
董荣华对记者讲,先进的循环用水系统提高了重钢新区供水循环率,减少了水资源费用和排污费用的支出,实现了吨钢耗新水量2.9吨水/吨钢的国内行业先进水平。
另外,重钢新区全厂办公、生活、洗浴等采用“太阳能 空气源热泵”供热技术,安装了2000多根太阳能真空集热管--这是全国规模最大的太阳能集中供热系统,其供热系统2/3能源来自可再生的太阳能,1/3能源来自通过高效热泵传递的空气热,日供热水(水温
重钢持续发展的“生命线”--产品创新
重钢在生产规模上没有优势,但一直有质量品牌优势。曾经以拥有国家金奖产品2个(16mnr钢板、
新产品开发方面,十年来,重钢紧紧围绕企业发展规划,以产品效益为中心,以市场需求为导向,以产品质量为重点,以产品系列化为途径,以微合金化为手段,扩大高附加值产品的试制规模,满足用户的需求,使新产品开发及特殊要求产品试制工作不断上台阶。 “十一五”期间,重钢加大技术开发部门的投入,对新产品开发及特殊要求产品试制执行更大力度的激励机制。这些举措有力地推动了新产品开发及特殊要求产品试制工作的进行。十年来,重钢共开发全新产品近60个,完成新产品试制410.34万吨,实现产值147.3亿元;《10#-37#系列欧标球扁钢的研制与开发》及《船用球扁钢系列产品研究与开发》获得很大成功,市场占有率居行业第一。
目前重钢自主开发新规格的船板不仅在量上暂时领先,而且在质上也有创新突破。2011年,重钢集团上下通力合作,重钢股份公司涉及船板研发、生产、质检、销售和运输的各部门密切配合,瞄准市场需求,调整产品结构,用半年时间自主攻克了
自主创新的种子,早已在重钢生根发芽,并初结硕果。2011年,重钢产钢603万吨、实现销售收入314亿元,一座年产650万吨钢的绿色钢城在三峡库区拔地而起;2012年1季度,重钢则以49.90万吨产量跃升为全国最大的船板生产基地,为“十二五”期间建设千亿企业赢得开局先机。
具有“中国钢源”之称的重钢,系中华民族钢铁工业的摇篮,传承着中国钢铁工业的血脉。其前身是清朝政府1890年创办的汉阳铁厂,至今有120余年的历史。“十二五”末,重钢致力于打造中国最大船舶用钢精品生产基地,销售收入将达1000亿元,成为中国西部重要钢铁基地,逐步向世界企业500强迈进。同时,职工年收入水平在“十一五”末基础上翻一番。
经过多年潜心经营,重钢“三峰”牌钢板被誉为“中国第一板”。2006年,重钢生产的船体结构用钢板和锅炉压力容器用钢板双双获得“中国名牌产品”称号,进一步巩固了“三峰”钢板在全国同行业的领先地位。重钢产品广泛应用于奥运鸟巢钢构、三峡工程发电机组构造、海洋石油钻井平台、以重庆鹅公岩大桥为代表的多座横跨大江南北的大型桥梁、以wsb号为代表的中国第一船、游弋在世界不同海域的客滚运输船舶、以深圳号为代表的系列战舰以及国庆60周年阅兵式上的装甲战车等。(通讯员 刘世华)